German Edge Cloud and INTRANAV are cooperating for the Digital Factory
German Edge Cloud (GEC) and INTRANAV are combining their expertise for the manufacturing industry. The Friedhelm Loh Group’s specialist for edge and cloud solutions will be working together with INTRANAV, the pioneer in hardware and software for real-time object location for the smart factory. Their vision includes track-and-trace applications for moving objects, products for intelligently controlled production lines and smart analytics services.
“Production processes and the associated supply of materials are extremely complex and highly interdependent. Only with transparent real-time data on all moving objects – from vehicles and materials to tools – can we optimise processes and guarantee quality,” explains Ersan Günes, CTO of IntraNav GmbH.
“We are pleased that we can now offer, among other things, location applications in real time for the manufacturing industry through our cooperation with INTRANAV,” says Dieter Meuser, CEO Cloud & Industrial Solutions at German Edge Cloud: “These applications run practically in real-time and with minimal delay times, based on our ONCITE solution. Furthermore, as an industrial IoT appliance centred on the edge cloud, it permits the operation of edge and cloud-based infrastructure solutions, as well as all the services needed for hardware, software and the platform.”
The location applications are based on a “Real-Time Location Data” technology stack (RTLS). In combination with INTRANAV's ultra-wideband and/or multi-RTLS stack, both companies' customers can now benefit from location accuracies of as tight as +/-10 cm in industrial environments. This means that users can precisely locate moving objects on their shop floor in real time – even in application scenarios with such complex factors as changing environments, interference from metal and harsh environments, and where other tough demands are placed on location accuracy and stability. For the user, this means transparency about where moving objects are and in what condition. This all makes it possible to optimise processes, achieve process reliability, and significantly increase efficiency.
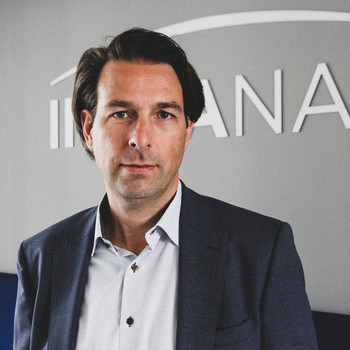
“We combine process virtualisation with real-time indoor track and trace data, as well as with digitised workflows that largely automate the manual processes on the shop floor.”
Andreas Radix, CEO of IntraNav GmbH
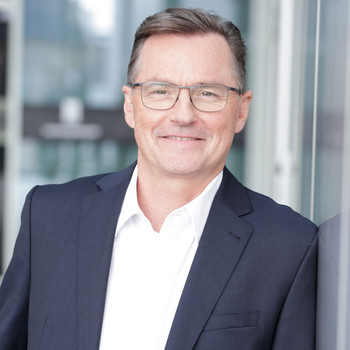
“With ONCITE, data is processed as close as possible to its point of origin. This way, huge amounts of data can be processed locally with minimal latency times; the results can be reported without delay. This is a basic requirement that lets us offer services like tracking and tracing,”
Dieter Meuser explains.
Controlling, analysing and optimising processes
The edge cloud-centric ONCITE industrial IoT appliance also includes cloud-native MES and MOM functionalities, which can be combined with the IIoT appliance's IoT services. Based on INTRANAV real-time location data, the applications can perform transaction control, data collection or analysis in real time, for example. A cycle of analytics, alerts and live dashboarding uses the data to generate insights and optimisations.
Bottlenecks, shortages and errors can be avoided and search times significantly reduced by integrating the high-precision INTRANAV real-time and sensor data. In this way, optimisation potentials can be identified on the production line while weak points and waste can be identified. Moreover, with retrograde analyses, those responsible can examine and optimise dwell times, throughput times, material flow analyses or, for example, the trails travelled.
GEC takes on 24x7 managed services for INTRANAV on the edge cloud-centric ONCITE industrial IoT appliance.
With end-to-end managed services, German Edge Cloud ensures the operation of application software and cloud management to ensure maximum availability and data security in INTRANAV projects.