Industry 4.0 put into practice: German Edge Cloud supplies smart solutions for Rittal's Haiger factory
At its Haiger plant, Rittal consistently manufactures keeping with Industry 4.0 standards. The world’s leading system provider for enclosure technology, power distribution, climate control, IT infrastructure, software and service has one of the latest digitally integrated enclosure manufacturing systems. Solutions from Rittal’s sister company German Edge Cloud are also used in the smart factory. A live dashboard system ensures transparency throughout the entire production process, enabling rapid intervention if necessary. A cycle of analytics, alerts and live dashboarding uses data to generate findings and optimisations.
Over an area of 24,000 square metres in Rittal’s Haiger factory building, more than 250 networked high-tech machines and system components are operating to produce roughly 8,000 AX compact enclosures and KX small enclosures every day. The machines and handling systems communicate not only with one another but also with higher-level control systems via Industry 4.0-compliant communication networks. Twenty driverless transport systems automatically take over transport duties within the factory. Packaging, labelling and finally, the handover to the neighbouring Global Distribution Center are also automated and networked – the foundation that allows Rittal’s customers to benefit from all the advantages of the digital twin.
Transparent production processes in the “Rittal Innovation Center”
System transparency must be ensured throughout the entire production process to maintain smooth operation in such a demanding environment. German Edge Cloud has developed the “Virtual Factory” solution – at the Rittal factory, it makes sure that all the important key figures and parameters are mapped in a live dashboard system. This shows – “live ” – the progress of production in terms of quantities, cycle times, the transport orders of the driverless transport system, as well as informing of bottlenecks, problems and malfunctions by issuing an alarm. This makes it possible for the operating staff to react or intervene quickly at any time.
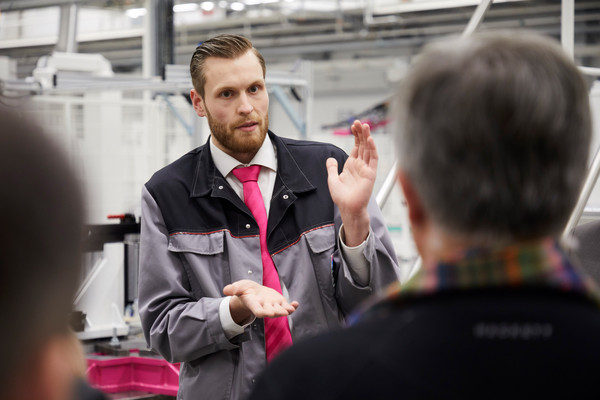
„For instance, we recently experienced an interruption on the packaging line. It was fixed within a minute thanks to the live dashboard system. Our plant managers and executives can immediately see how long a line is automatically stopped, whether there are any open transport orders for the driverless transport system and at what level the quantities are per day and per shift,”
says Moritz Heide, Head of System Maintenance and Work Preparation at Rittal's factory in Haiger. He continues:
„This gives us greater transparency and complete control across all the units and systems in production, which in turn leads to big gains in efficiency.“
The live dashboard system is based on the ONCITE edge cloud application from German Edge Cloud. This makes it possible to monitor and support production by providing data and analysing the current production and production planning situation. It also displays warnings in the event any issues or problems arising. ONCITE thus forms an active part of production control, and it can also be integrated into supply chain planning. The connection of SAP ERP to ONCITE is planned as a next step, so that Rittal can view the stock levels and display availability information for orders.
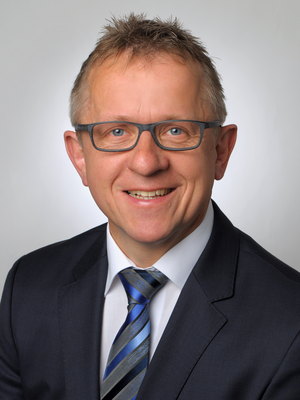
Drawing insights from data and automating pro-cesses
Rittal’s factory uses in addition a data analytics solution from the German Edge Cloud. To this end, a programme was created involving analytics, alerts and live dashboarding. Sensor values and data, for example, from the packaging line, stem from the live dashboard system. Regression analyses, for instance, are used for data analysis.
On this basis, the process experts can establish relationships, such as that between the temperature and the probability of malfunctions. Alerts can be derived from these, for example: “Whenever the temperature rises above Y in situation X, an alert appears on the live.”
„With the Data Analytics solution, we are currently creating the basis for predictive maintenance – another crucial component on the way to self-controlling production“
explains Bernd Kremer, COO Digital Industrial Solutions at German Edge Cloud.