Streamlining the value chain: Dataspaces as opportunities for tapping into the potential of digital transformation
The industry is still feeling the pressure to change. Streamlining processes to improve efficiency and productivity will establish companies’ future competitiveness. So how can decision makers for machinery and panel building contribute to withstanding this pressure while simultaneously tackling and managing the energy revolution and digital transformation? At the SPS in Nuremberg, Rittal, Eplan, Cideon and German Edge Cloud will provide answers and show why streamlining and automating entire value chains as a key driving factor points the way to the future of the industry.
Economic activity never takes place in a vacuum. The industry, in particular, has constantly been exposed to global change and crises, and is thus always under great pressure to change. Nevertheless, how should companies prepare themselves for current and future situations? How can the step from crisis management to the long-term transformation in digitisation and energy transition, along with a shortage of skilled workers be mastered and regarded as an opportunity for the industry? At the SPS in Nuremberg, Rittal, Eplan, Cideon, and German Edge Cloud (GEC) aim to discuss all these topics with attendees and show options for panel building, switchgear and machinery based on their respective competencies.
Factory of the future: Digital twins for smart production and power management
Smart production – economic production with highly automated and efficient processes – is required. At the same time, this must be managed in an energy-efficient way, and with flexible solutions that can be adapted to individual customer needs. And all this against the backdrop of a shortage of skilled workers.
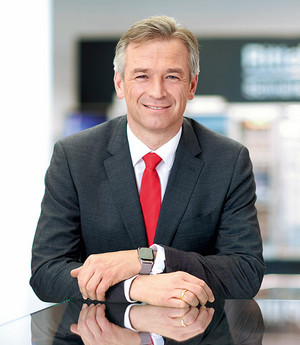
“Nowadays, innovation means making the customer’s overall performance more efficient and successful. If we no longer think only in terms of products and solutions, but also in terms of process optimisation, we can only do so by cleverly combining both hardware and software.”
says Markus Asch, CEO of Rittal International and Rittal Software Systems.
As enablers of smart production, the four companies will be demonstrating at the trade fair how it will be possible to connect the ecosystems of automation, products and production via one respective digital twin. This will make smart production processes more transparent and efficient. In addition, the energy flows also become transparent – a critical success factor for industrial companies both now and in the future. Therefore, energy transition acts as an accelerator for fundamental changes in the industry.
Visitors to the trade show will be able to observe practical implementation not only based on Rittal’s own Smart Factory as an example, but also in the form of an Intrafactory track & trace software application in the Smart Press Shop in the city of Halle an der Saale. This joint venture between Porsche and Schuler uses the Schuler Digital Suite with track & trace. It is based on the Catena-X certified ONCITE DPS. This provides the basis for using data in the future for internal factory processes and quality optimisation through the Catena-X “Cofinity-X” operator platform. Correlation analyses on the painting and final assembly lines can further minimise scrap.
Streamline the value chain
How can control systems and infrastructure be created more quickly? Here, the trade fair booth will focus on data consistency across the entire value chain – from electrical design and planning through system technology supply and panel building to the digital operations phase of the systems. Panel builders and switchgear manufacturers save time and money in their value-added process with solutions from Eplan and Rittal. As a guarantee of seamless system data for maintenance, smart service and system connectivity, they will also become sought-after digital partners for system operators.
Adding value across the boundaries of the exhibition booth
Rittal and Eplan will demonstrate practical implementation across company boundaries with a new type of robot for control wiring, and linked exhibits to neighbouring stands. A fully automatic Rittal Wire Terminal WT C machine at the booth assembles the wires live and sends them to remote workstations by compressed air using the prototype of a wire handling system. A robot prototype from Rittal Automation Systems then wires control components there fully automatically. The ‘wire post’ also crosses the borders to the neighbouring stands of partner companies, where the wires are further processed at Rittal workstations, digitally assisted by Eplan Smart Wiring. The basis is the data consistency in Eplan’s industrial automation ecosystem and the high data quality of the components from the component manufacturers in the Eplan Data Portal.
The mechatronic parts list is becoming a reality
Data consistency is also the key to the new eCAD connection (Eplan) to Cideon Conify. Mechanical engineers can automatically generate design data and parts lists using a product configurator. The parts list can be output mechatronically and in sync with mechanics and electrical engineering. And, using EEC, circuit diagrams and electrical documentation can also be generated with a mouse click. At the SPS, Eplan will also show machine cabling via digital twin using Eplan Harness proD and the innovations of the Eplan Platform 2024 with its electrical, fluid, measurement and control technology and enclosure construction systems.
Accelerating the expansion of the energy infrastructure
Process streamlining is also set to advance the energy transition and the industry, which is facing intense pressure. The expansion of this infrastructure must pick up speed to meet industry requirements: “Modularisation, standardisation and data consistency are our driving principles,” explains Markus Asch: “We need to harness the potential that lies in optimising and industrialising process chains. End-to-end hardware and software solutions are speeding up the expansion of the infrastructure, from energy generation and storage to grid expansion and sector coupling to transformer stations and electric vehicle charging parks. The efficiency gain reduces costs, while the data, as the automation twin, opens up further possibilities for use in operation.”