What the smart factory needs today: Consistently networked ecosystems
The objectives of industrial transformation are clear: It is all a matter of more transparency, speed, and sustainability in manufacturing and operation. Digitalisation and networking of the industrial and IT ecosystems is here a prerequisite: For machine and plant engineering, automation, and IIoT solutions, IT infrastructures, and smart services. At the Hannover Trade Fair 2022, Rittal, Eplan, and German Edge Cloud – for the first time together on a joint stand – will be showing you how they integrate these different worlds and support businesses on the road to a smart factory. A particular focus is placed on solutions for the efficient, secure and sustainable operation of machine systems and manufacturing processes.
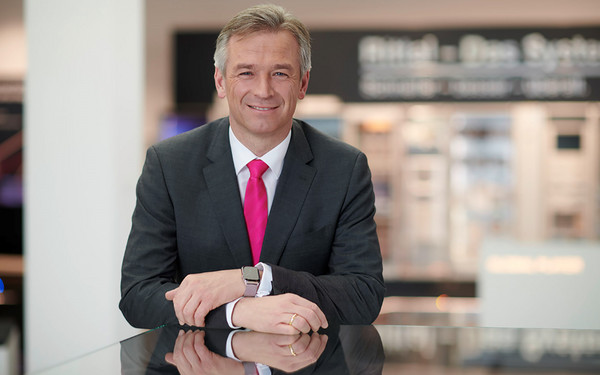
“If companies want to manufacture their products sustainably, cost-effectively and with ultimate speed and flexibility, they need to implement digitally integrated production and consistent networking of their processes and ecosystems,” says Markus Asch, CEO of Rittal International.
The smart factory, with its AI, real-time, 5G, and Industry 4.0 applications, is still a future dream for many companies. Practical experience in the manufacturing industry indicates that even after almost ten years of “Industry 4.0”, there’s still plenty of potential for digitalisation. In fact, for many manufacturing companies, it’s only now – after they’ve spent time learning – that things are getting going, but even by taking the first steps in this direction, they can achieve benefits.
“If companies want to manufacture their products sustainably, cost-effectively and with ultimate speed and flexibility, they need to implement digitally integrated production and consistent networking of their processes and ecosystems,” says Markus Asch, CEO of Rittal International. “The Friedhelm Loh Group combines the industrial experience and technology know-how of Rittal, Eplan and German Edge Cloud to overcome frequently perceived boundaries between the worlds of machine and plant engineering, automation, IIoT and IT, and to unlock further potential for customers by bringing these worlds even closer together.”
The joint presentations place a particular focus on solutions for the efficient, secure and sustainable operation of mechanical systems.
Digital workflows: From engineering to maintenance
The Eplan platform, as an engineering system built around standardised data, interfaces, and complementary cloud services, realises an integrated and transparent workflow along the entire value chain – from engineering, via manufacturing and commissioning, through to plant operation. Solutions provider Eplan is presenting the current Eplan Platform 2022 with its object-oriented data management functions, the new “Insert Center” and cleverly integrated cloud solutions. Hannover is at the same time an opportunity for interested visitors to catch a first glimpse of the upcoming Eplan Platform 2023, which will greatly simplify the handling of circuit diagram macros in respect of international norms and standards. A new graphics engine and a central device management system are further innovations awaiting the trade public. Novelties such as the Eplan Data Portal request process, through which companies can order standardised data for individual devices via a credit system, are likewise on the agenda.
The showcase of a roller conveyor demonstrates how companies can benefit from a fully digitalised engineering database – also in case of a machine breakdown, where the source of a problem must be found as quickly as possible. In such scenarios, cloud solutions from Eplan are backed up with technologies from the Industrial Internet of Things (IIoT) and the field of augmented reality (AR).
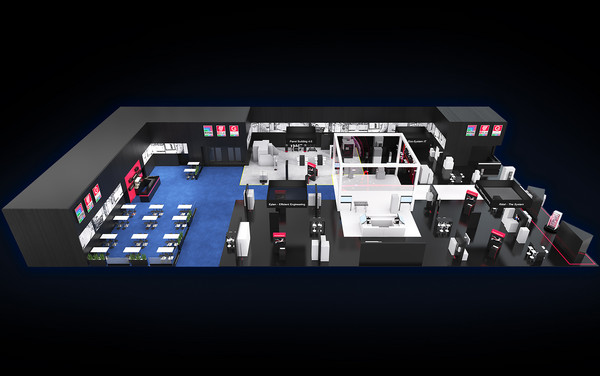
At the Hannover Trade Fair 2022, Rittal, Eplan, and German Edge Cloud – for the first time together on a joint stand – will be showing you how they integrate IT and industry and support businesses on the road to a smart factory.
Enclosures in the cloud
To ensure that relevant panel building and switchgear manufacturing data are always up to date, Rittal has developed the new digital wiring plan pocket “Rittal ePocket”. A QR code on the enclosure permits access to the complete equipment and system documentation, including the digital twin in EPLAN Cloud, which is always up-to-date over the entire service life. Service and maintenance staff can directly access up-to-date wiring plans right on the system with a smartphone or tablet. This ensures quick troubleshooting in the event of repairs and maintenance.
Cooling systems and services for more sustainability
The energy-efficient, sustainable operation of control systems and switchgear is another key issue. Therefore Rittal will be unveiling its new Blue e+ S cooling units, which initial test installations have shown to be up to 70 per cent more energy saving compared with previous solutions due to efficient hybrid cooling with a passive heat pipe. A new refrigerant further reduces the Global Warming Potential. Also incorporated are technologies to enable networking with service offers. Rittal Smart Service permits the visualisation of the operating characteristics of cooling units. Rittal Smart Service enables the visualisation of the operating characteristics of cooling units. Data are communicated in real-time to facilitate the planning of required maintenance and to ensure that critical errors are detected as early as possible. Automated processing of the cooling unit data lays the foundations for fast error rectification – and thus maximised machine availability.
Full transparency in production
Solutions geared specifically to machine operation are not alone in the spotlight. German Edge Cloud points out that even the first steps towards digital transformation offer significant opportunities for the optimisation of existing manufacturing structures. Taking the example of the new Rittal factory in Haiger, the IIoT specialist will be showing how data can be used in an intelligent production environment designed according to Industry 4.0 principles. More than 250 high-tech machines and plant components are networked with each other, while the digital production system, Oncite, enhances transparency and expands the possibilities for plant and system control based on data analyses. This all helps production managers to recognise developing bottlenecks, problems, and disturbances in good time and to intervene immediately.
Rittal’s RiMatrix Next Generation offers a future-proof, modular infrastructure solution for data centres of all sizes and requirements as the backbone of all IT applications. A modular, end-to-end system that covers rack, power, cooling, security, and monitoring, can be used to build customised solutions for all IT scenarios easily and quickly. Everything from the rack, rack edge, enterprise, and colocation data centres to hyperscale data centres can be configured. A showcase for 3D data centre planning and construction introduces the latest solutions from the Rittal Competence Centre. One particular highlight is the all-in-one OT solution of a Rittal data centre container with innovative Blue e+ outdoor cooling units, which enables outdoor expansion of an existing IT infrastructure based on resource-sparing, cost-effective, and energy-efficient cooling technology.
To simplify and accelerate the selection and procurement of system solutions in enclosure technology, Rittal is offering digitised sourcing processes and tools like the new RiPanel Configurator and the Online Shop. The key to accelerated processes lies in the standardised “Rittal – The System.” platform, with enclosure, climate control, and power distribution technology. Innovations include the VX SE free-standing enclosures, AX compact enclosures made of plastic, VX25 TopTherm chillers, and the VX25 Ri4Power system for accidental arcing protection (class A and B). Furthermore, Rittal is presenting the latest solutions for implementing energy storage and charging infrastructure systems.